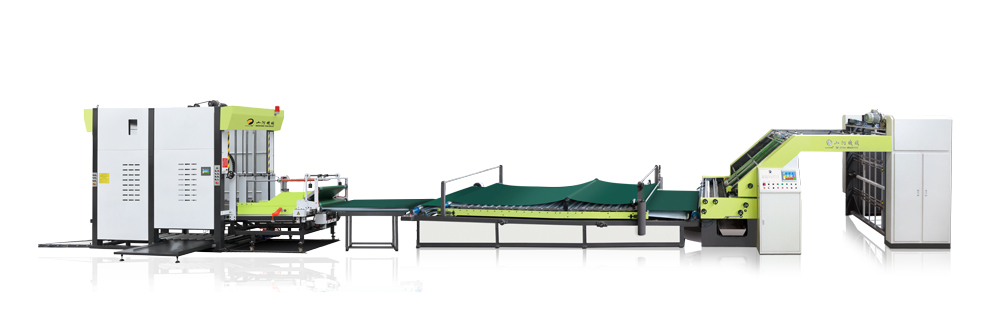
A. We manufacture this 3rd generation model with a new structure and a new concept, and promote the design of the machine on the premise of intelligence, digitalization and integration. The machine is fully servo control (digital input) and linkage control.
B. One-touch control function: The automatic adjustment of the machine from the front and back of feeder, the size of the alignment, the size of the top sheet conveying, the size of the bottom sheet conveying, the whole roller pressure, the glue thickness, the front gauge position, the paper interval, to the front and back of press part is adjusted by one touch when the machine is started. And the advanced function is a one-touch linkage paper stacker. After the host enters the paper size, the paper stacker does not need to enter again, and the paper stacker can be adjusted directly with one-touch, so as to truly realize intelligent automatic control and digitalization.
C. High speed and high efficiency: the max. speed is 200 meters/min, and the max. speed is 20,000 sheets/hour according to 500mm paper.
D. Reinforced structure: the wall plate of the flute laminator is thickened to 35mm, and the whole machine is heavy to ensure high-speed and stable operation.
E. Servo shaftless high-speed feeder, which is added to the one-touch adjustment function, making the paper feed more accurate and more stable.
F. The alignment has also been added to the "one-touch start" function, which can be fine-tuned at any time. The new dual-purpose whole board paper structure can push the whole board paper onto the paper feeding part of feeder, which greatly reduces the time and work. The paper can also be prepared and propelled along the track, making safety equipment for customers who need to organize the paper.
G. Bottom paper conveying part (Optional):
1. Front edge type (sun wheels are driven by servo motor with strong air suction):
Its large blowing flow rate and increased paper feeding friction are more conducive to the smooth delivery of warped, rough, heavy, and large size of the bottom paper. Unique detail design: Each servo rubber wheel is equipped with one-way bearings to ensure accurate delivery and reduce wear. The paper feed rubber wheel has a long service life, which can reach 5-10 years, thereby reducing the labor force of replacing the rubber wheel and after-sales costs. This type is suitable for any corrugated board, and is more suitable for multi-layer cardboard laminating. (The right cylinder can be added to pat the paper)
2. Belt conveying type (punched belts are driven by servo motor with strong air suction):
The corrugated board is smoothly transported by the perforated belt, which is especially suitable for the lamination between colorful printed paper and corrugated board (F/G-flute), cardboard and grey board. The bottom paper will not be scratched during delivery.
H. Paper feeding roller: Model HBF equipped with slotted roller (diameter: 100mm), its advantage is low noise and no paper jam. Model HBF-3 is equipped with a spiral flattening steel roll (diameter: 150mm) with a pattern, which has the advantage of making the bottom paper stretched and flat, easy to glue, and will not wrinkle.
I. Model HBF-3: The pattern roller used for glue is made of stainless steel, which is carved by laser and has shallow lines. Its diameter is increased from 125mm to 150mm, and the rubber roller matched with it is increased from 100mm to 120mm, so that the area of glue becomes larger. The effect of the change is that the angle between the two rollers is larger, the amount of stored glue is larger, which makes it difficult to have the problem of glue splashing and flying, and the machine runs more high-speed and stable.
J. The press roller has been upgraded from the original diameter of 100mm to 150mm, which is more conducive to the laminating of the top sheet and the bottom sheet.
K. All bearings on the left and right sides of the host seat are improved to double bearing structure, which can effectively extend the service life of the bearing. With automatic oil supply system, it is easy to maintain the machine, and the bearing is not easy to damage.
L. Automatic glue adjusting device, which automatically adjusts the glue thickness according to the set standard, and can also be fine-tuned by touch screen.
M. Automatic pressure adjustment, which automatically adjusts the pressure of the whole machine according to the set standard, and can also be fine-tuned by touch screen.
N. The space of the bottom paper part is 3 meters long, which is conducive to the loading, stacking and operation of the large size bottom paper.
O. The whole machine is the European version of electronic control, using the Parker (USA), Siemens (Germany), Yaskawa (Japan) and Schneider (France) and other international top electrical equipment configuration, its excellent performance to ensure stable and efficient output of equipment.
P. The machine adopts the motion controller(Parker, USA) shaftless control to achieve direct signal transmission, with no interference, no change, stable and accurate advantages. (At present, some machines on the market use 5G signal transmission, and there are problems such as interference from the working environment or received communication signals, which are difficult to eliminate and solve on the spot, and 5G transmission has side effects such as leaking production data.)
Q. PLC (Siemens, Germany) precise control, when the bottom sheet does not come out or the two top sheets are joined together, the host will stop to reduce the loss. More than 30 years of experience in laminating machine production makes the programming system more stable and the laminating precision is higher.
R. The machine uses photoelectric detector (P+F, Germany), and the color of the top sheet and the bottom sheet are not required, especially black can be recognized.
S. The design of the equipment considers from the safety point of view, and each key position is equipped with induction, alarm and shutdown, which effectively avoids security risks and illegal operations. In particular, double grating is installed in the paper stacker, and the first-level alarm warning personnel shall not enter to affect the normal production, and the second-level alarm will stop immediately to protect personal safety. Each part is also equipped with a protective cover, safety warning signs, and emergency stop buttons according to the requirements of exports to Europe.
Post time: Dec-16-2023